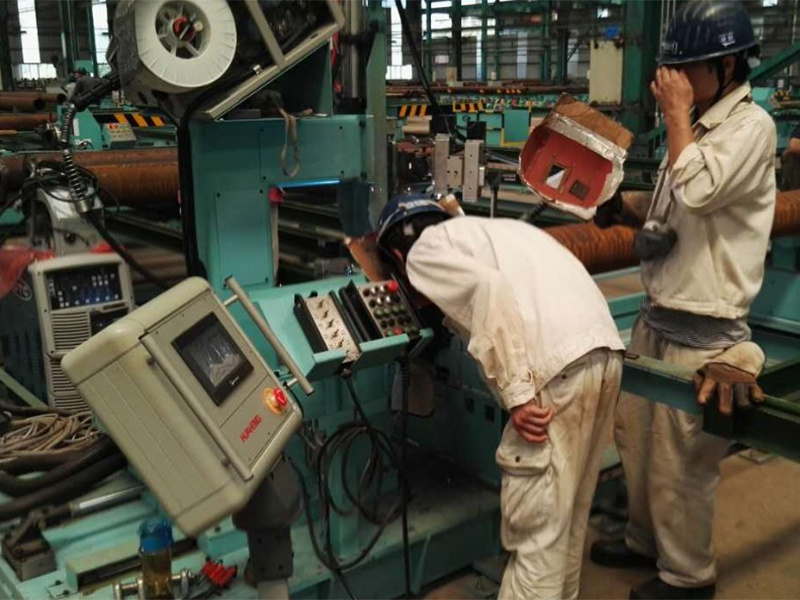
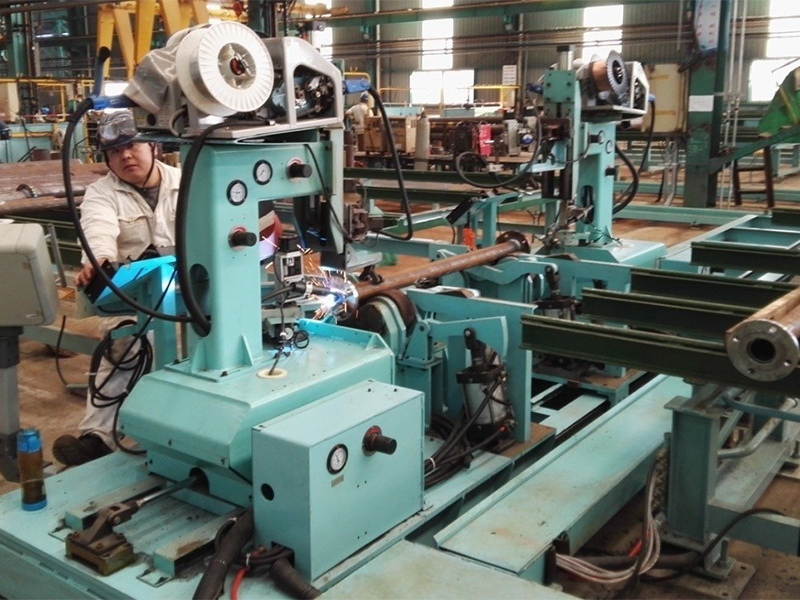
Medium diameter straight pipe flange four-point welding system
Classification:
Key words:
Arc Welding Technology | Robotic System Integration | Automation and Intelligent Manufacturing
Detailed description
This equipment is used for automatic welding of the inner and outer mouths of single or double flanges or the outer mouths of casing of pipes that have been pre-spot welded, in the form of single flanges, double flanges, single casing, double casing, one head of flange and the other head of casing and other forms of pipes. The equipment has the function of manual or automatic welding of the inner mouth of the casing.
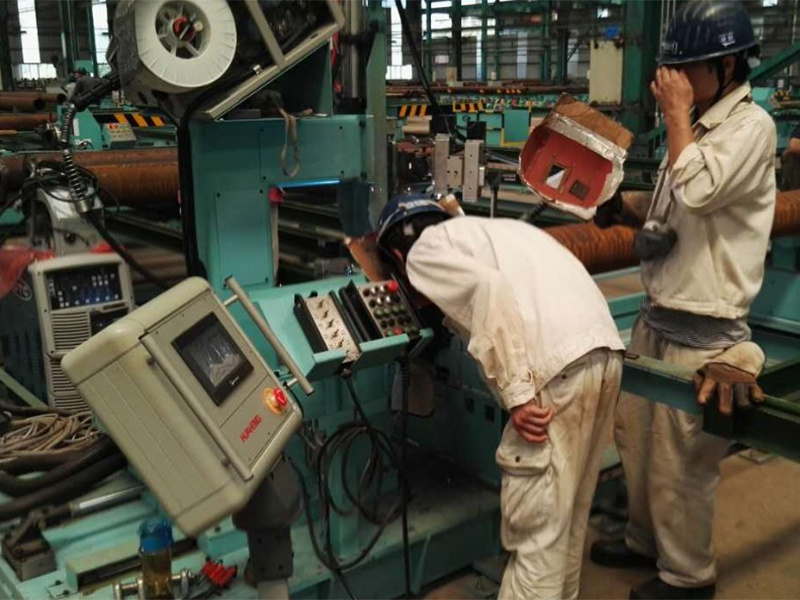
The system needs to consider accepting the processing process data information from the real-time control system of the computerized pipe processing system for on-line production and synchronized operation with the previous processing process. Can also accept processing data files, offline mode of independent production operation. When running, according to the accepted processing information, will be located in advance in the straight pipe flange welding machine feeding frame to be welded pipe through the shift, complete the welding process.
Each end of the flange welding machine is equipped with a set of operation display device, which can realize various welding functions such as adjustment of torch position, voltage and current adjustment, start-stop control, etc. at both ends respectively.
-Applicable range of welding equipment
Pipe caliber range: DN65-DN200;
Pipe length: 0.8-6 meters;
Casing shrinkage range: 50-75mm;
Pipe wall thickness: 5-15mm;
Pipe length: 800-6000mm;
Flange specification: 6kg, 10kg, 16kg;
Casing specification: through-hatch casing, connecting casing;
Height of feeding end: about 660 mm; Height of discharging end: about 600 mm; (Parameters to be determined after the completion of matching specifications).
Production capacity: single person operation (including loading, welding, discharging) 8 PC / hour (accessories 10 PC / hour) to provide loading, tuning, welding, unloading of the timing diagram; (loading time of about 10 ″, tuning the gun preparation time of about 30 ″, welding time of about 2 ′ 30 ″ (DN125 single welding time to DN125 single welding time calculations), unloading time of about 20 ″.
Driving method: electric drive;
Operation method: one-button start operation;
Speed adjustment: Adjustment button or knob;
Pressing method: automatic pressing by mechanical wheel;
Institutional requirements: self-contained logistics structure to meet the front and rear processes of automatic flow handling;
Scope of use of welded parts: DN65 DN200 pipe flange and casing;
-Brief description of the operation process
according to the length of the pipe electric movement of four-point welding equipment mobile end to the appropriate position;
welded pipe fittings overflow to the roller frame, moving the welding gun holder to the appropriate position;
press the pipe to prevent tampering;
adjust the two sides of the double gun welding point position as well as set the welding machine current, voltage and other parameters;
Select one side or two sides of the target welding gun to start starting automatic welding;
After the welding is completed, turn over the flow to the finished product material rack.
-System Features
A high degree of system integration provides a strong guarantee for the realization of professional automated production with high efficiency, high quality and low labor intensity;
Four guns can be welded at the same time, the welding efficiency is very high, allowing a certain deviation of the tube ellipticity (the smaller the tube the more difficult it is to weld four guns at the same time, there is a heat accumulation problem);
Stable and reliable imitation mechanical tracking method, welding process reduces manual intervention, high degree of automation, solves the problem that small pipe diameter has certain ellipticity which can't be welded by four guns at the same time;
Huaheng's perfect system and mature welding process strongly guarantee the high quality of weld seam, that is to say, it improves the welding efficiency and also guarantees the product quality;
The components of the control adopt the products produced by international brand companies, such as Schneider, Emerson, Siemens and so on;
The controller adopts programmable PLC controller with friendly and intuitive interface and good control stability;
Building blocks modular design, reduce system design and production cycle, conducive to large-scale production or maintenance;
Stable system ensures the quality of the product as well as the turnkey project.
-Configuration list
NO. | Equipment Name | Quantity | Remarks |
1 | Pipe flange four-point automatic welding machine | 1 set | Huaheng, servo traveling |
2 | Welding power source (including wire feeder) | 4 sets | With OTC |
3 | MAG welding torch | 4 sets | Huaheng |
4 | Welding torch swing control device (including motorized cross slide) | 4 sets | Huaheng |
5 | Mechanical profiling tracking device | 4 sets | Huaheng |
6 | Automatic welding control system (Huaheng Pipeline Control Technology Software V1.0, software copyright) | 2 sets | Huaheng |
7 | Cable assembly | 1 set | Huaheng |
-Introduction of four-point automatic welding machine for pipe flange
Pipe flange four-point automatic welding machine is mainly composed of base, roller frame, welding operation frame, movable traveling structure and other components. Roller frame and welding operation frame are placed on the movable traveling structure to move to the corresponding position according to the length of the workpiece, and the power supply and control box are also placed on the electric traveling mechanism to move randomly. The welding torch, electric cross slide frame and so on are arranged on the welding operation frame.
The workpiece is sent to the rotating roller frame through the feeding trolley, and the welding torch operating frame at both ends is tightened against the flange surface of the workpiece through the leaning wheel under the thrust of the cylinder, and the welding torch mechanism is moved to the flange surface, so that the preparation of the welding torch is basically completed.
The entire welding torch operating frame is mounted on a movable traveling mechanism that can move with the length of the workpiece. Before welding, there is a wheel below the operating frame, through the cylinder will be the entire operating frame to use the wheel to tighten the workpiece, the role of the pneumatic wheel is to prevent the workpiece in the axial fluctuation.
The height of the external welding torch is raised and lowered by the operator, and is raised when the pipe diameter is different. The left and right side of the operating frame is exactly the same, through the panel can choose whether a grab, two guns, or four guns at the same time arc welding.
When welding pipe flanges of different pipe diameters in batches, you can just adjust the spacing of the roller frame and the operating height of the welding gun.
There is a linear guide rail installed on the crossbeam, and the mechanical mold device can move freely on the crossbeam, and the welding gun oscillator, gun adjusting mechanism and welding gun are installed on the mechanical mold device.
When the equipment is running, there is a warning light flashing on the column of the operator.
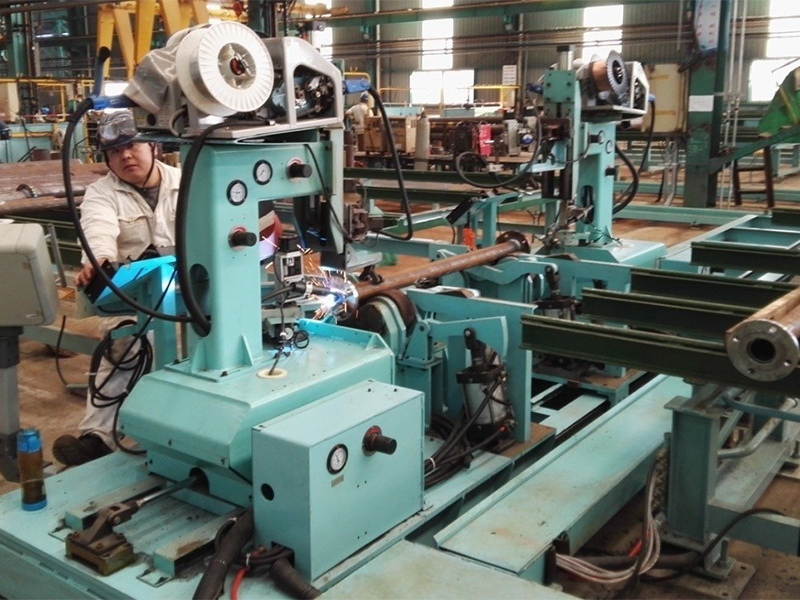
Inquiry
Xuzhou Huaheng Robotics Co., Ltd.
Phone: 0086-516-66882288
Kunshan Huaheng Robotics Co., Ltd.
Phone: 0086-512-87880678
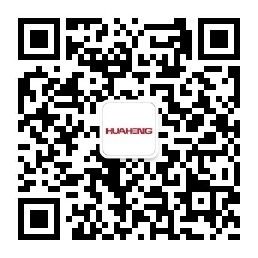
Focus on Robot Division
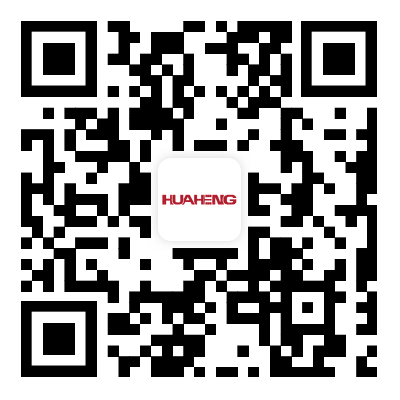
Huaheng mobile phone terminal
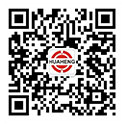
Huaheng Company Public Number
Copyright © 2024 Xuzhou Huaheng Robotics Co., Ltd. All Rights Reserved